products for renewable fuel plant
highlights
- Aalberts integrated piping systems and BROEN sourced and delivered valves to the world's largest renewable fuel plant in record time
- the two companies were able to deliver twice as fast as the nearest competition
- the project will help the customer work towards its goal of producing up to 800 million gallons of renewable diesel, renewable gasoline, and sustainable jet fuel annually
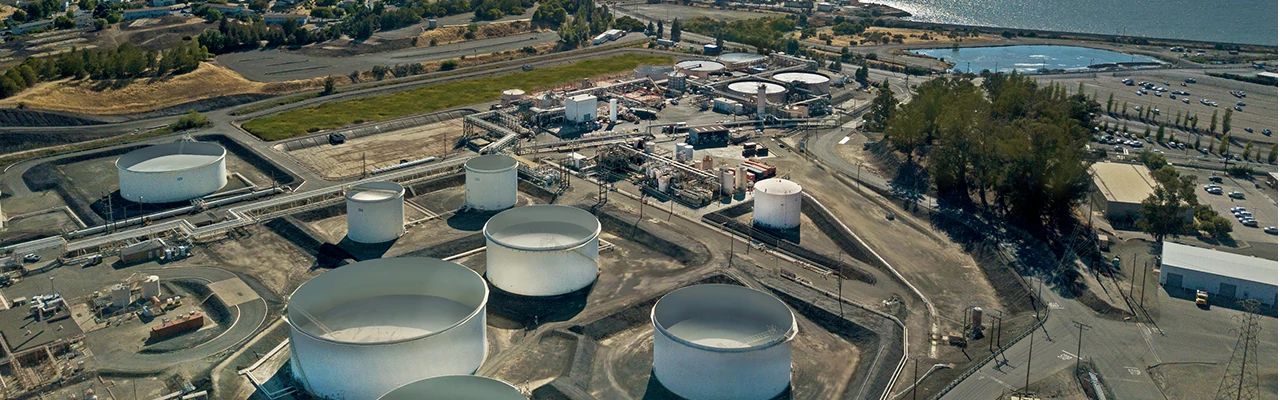
Aalberts integrated piping systems and BROEN sourced and delivered specialty ball valves for the world's largest renewable fuel plant, helping the operation on the United States’ west coast meet its time-critical targets.
true specialists
“Our client was developing the world's largest renewable fuel plant in the United States, which will be capable of producing up to 800 million gallons of renewable diesel, renewable gasoline, and sustainable jet fuel annually,” says Kyle Spangler, global director of product management (Valves) at Aalberts integrated piping systems. “They needed two very specific types of ball valves, and Aalberts was able to deliver in record time, solving two key issues for the customer.
First, Aalberts is one of very few companies that can supply both the lower volume high-end specialty ball valves that are manufactured by BROEN and the higher volume general service industrial valves that are manufactured by Aalberts integrated piping systems. Second, the customer needed the valves as quickly as possible. While the next best lead time offered by the competition was 30 weeks, we were able to deliver in 14 weeks. In the industrial market, lead time is critical and enables us to demand a higher premium for our product.”
ultimate flexibility
As well as delivering the products well ahead of anyone else in the market, Aalberts was also able to ensure market shortages of a key material didn't lead to any delays. “The customer had requested PCTFE, but there is a global shortage of this material at the moment. Being able to offer TFM as an alternative allowed us to quote a shorter lead time and still meet the requirements of the application. The TFM seats are manufactured in our Conway facility, so we were able to secure the supply chain for this material and offer a reduced lead-time, utilizing our in-house production capabilities. Looking ahead, we see opportunities to continue with this type of collaboration to capitalise on market growth from the ongoing energy transition both in the United States and abroad,” Kyle says.
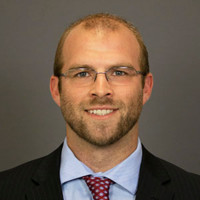