surface technologies for strategic industries
highlights
- RMF, developed a robotic treatment technology with options for topcoats, sealers or waxes over zinc and zinc nickel electroplating
- the robotic treatment technology will substantially improve the processing time and therefore increase mission-critical abilities
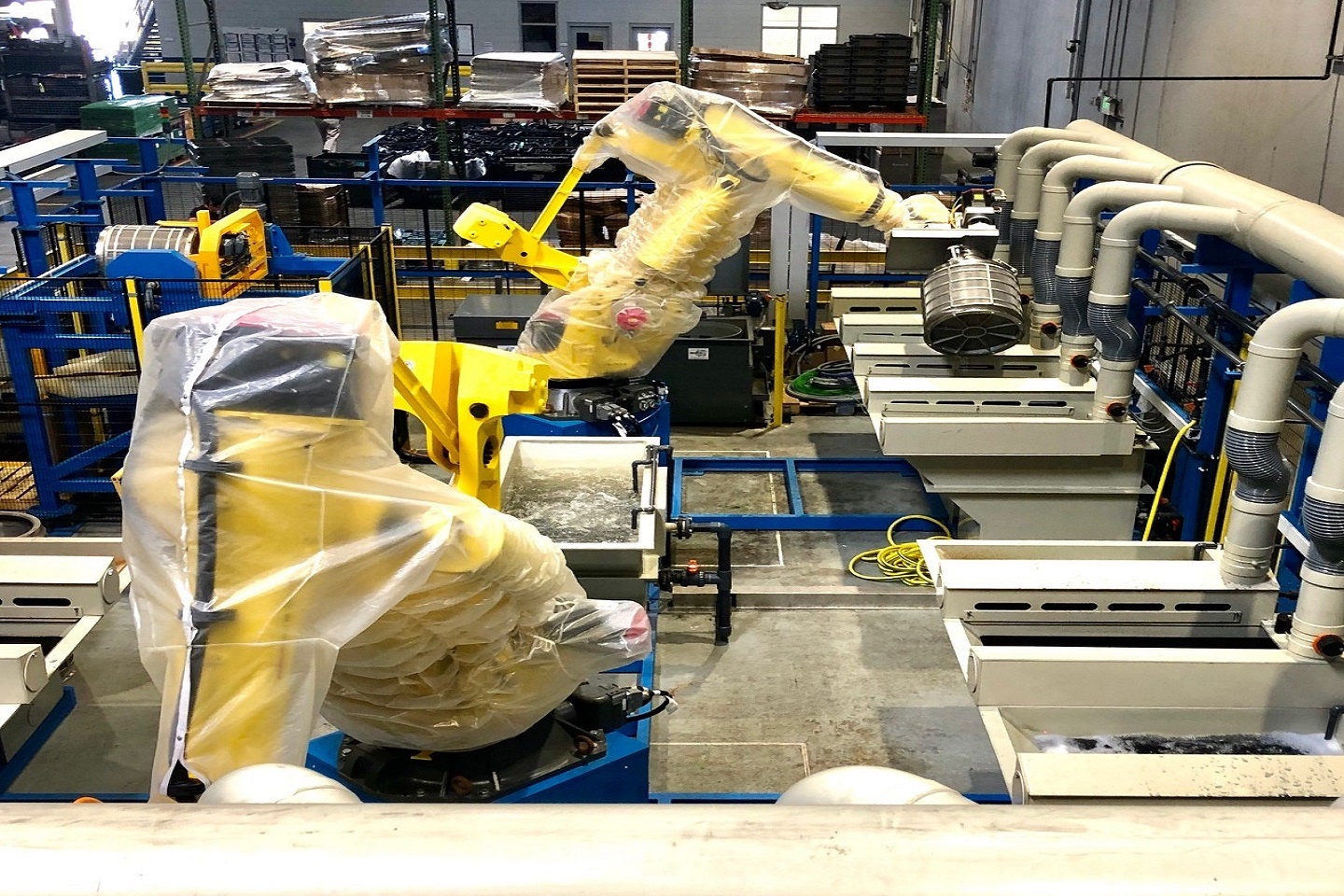
Across Aalberts, we are always launching new technologies to help customers advance their business. It is this focus on creating mission-critical solutions that helps highlight our unique strengths.
RMF, part of Aalberts surface technologies in Greenville, South Carolina, has developed a SIDASA robotic treatment technology for post-plating and baking applications of trivalent passivates, with options for topcoats, sealers or waxes over zinc and zinc nickel electroplating.
cutting-edge solutions
“The new process gives us a technological advantage within our supply chain,” explains the director of product & business development, Adam Brumfield. “Historically, the post-treatments were applied manually, but this is the first time we’re implementing a robotic solution. The main advantages for us are reduced costs, increased speed of delivery, and greater efficiency, as we can run the machine 24 hours a day. It also improves consistency and quality.”
strategic industries
And with key customers in the automotive and agricultural sectors, increased uniformity is a vital quality. “This technology drives our competitive advantage because we can minimise surface defects. It also makes it more attractive for local companies in the southeastern United States, where we are based, to start working with us. Traditionally, these companies would ship their parts hundreds of miles to be processed, but this technology means we can offer high-quality results more cost effectively.”
With the company providing treatment on fasteners and other components for the mobility industry, they typically need to process orders quickly. “The turnaround time is expected to be within 24-72 hours, so the robotic treatment solution will substantially improve our processing time for those that need it, increasing our mission-critical abilities,” Adam says.
Innovation and growth go hand in hand at Aalberts, and we are proud to see we are making such strong progress in our own specialised areas.
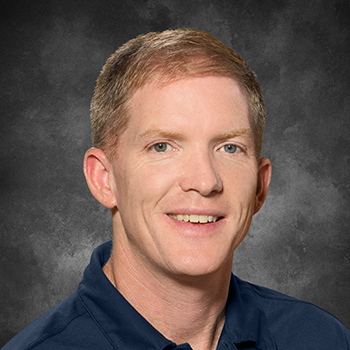