moon landing technology
highlights
- Aalberts fluid control developed an electronic pressure regulator to be used in a customer’s unmanned moon landing
- existing quality data and experience gained in the automotive sector, was used for this application
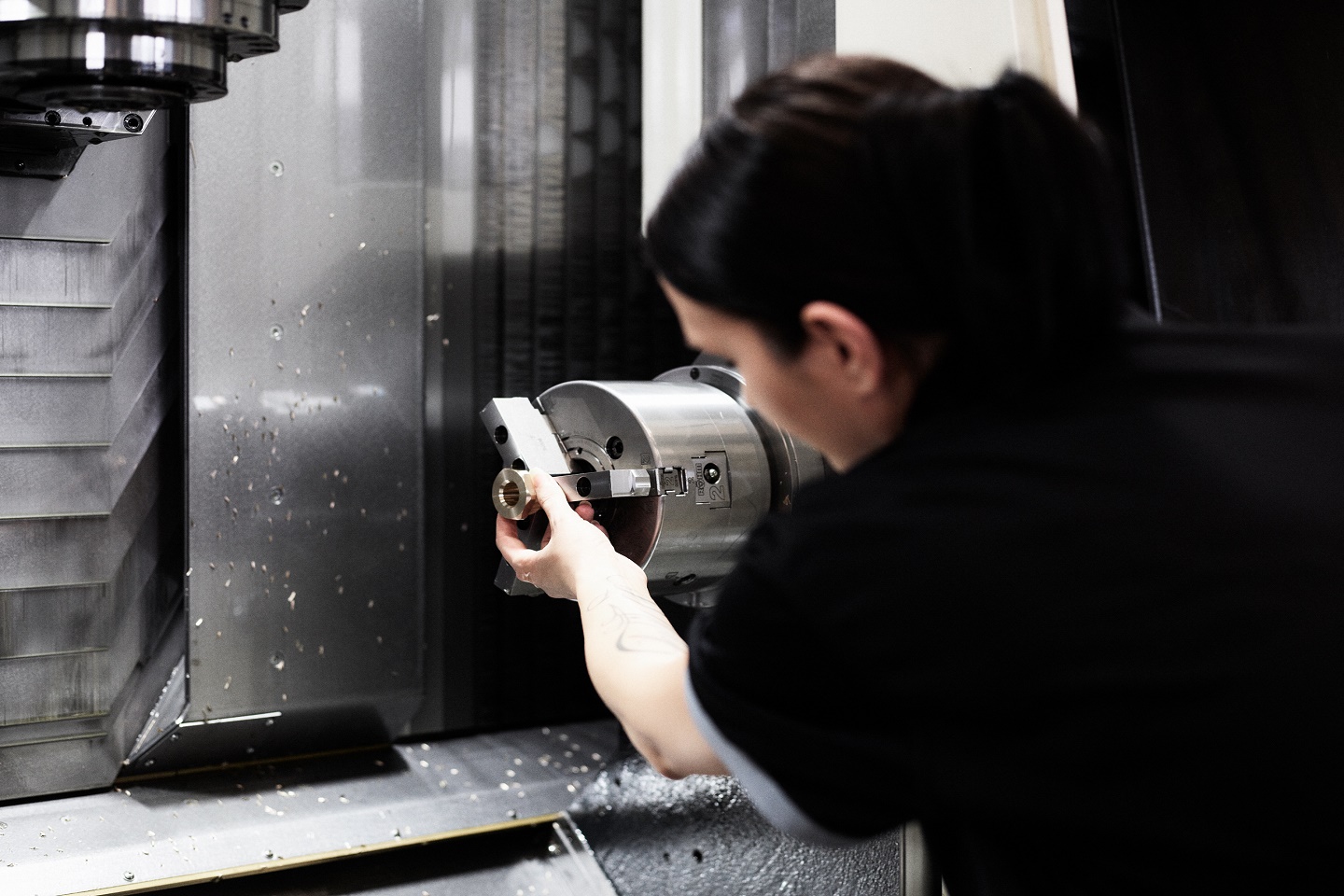
Making it to the Moon takes ingenuity, precision, and dedication. Which is precisely why Aalberts fluid control was commissioned to develop an electronic pressure regulator to be used in a customer’s unmanned moon landing.
modern space race
While the original space race took place between the USA and Russia in the 1950s, space exploration today includes a number of private companies sending up satellites and preparing to develop space tourism. With this change comes the need to cut the extreme development costs, without compromising on the exceptionally high quality and safety requirements.
cross-sector specialisation
One way to achieve this is to look for potential synergies across other sectors, such as the automotive industry, to make use of existing expertise. A customer asked Ventrex to develop a more flexible solution for regulating pressure in the fuel supply of modules to be used in a mission to the moon. They were aware we are market leader in the development and series production of electronic pressure regulators, which is why they asked us to devise a solution as closely related as possible to our automotive volume production counterpart. This enables us to leverage existing quality data and the experience we have gained in the automotive sector, which in turn means that risks relating to the functionality and safety of the project remain minimal and easily manageable.
functional prototype in just 15 weeks
The expertise and commitment of the project team made it possible to create a functional prototype, which fulfilled all the customer's requirements and was ready for further testing, within just 15 weeks. The pressure regulator we developed for the landing module provides a high level of flexibility in relation to fuel supply, achieved through the ability to control fuel flow electronically. The developed valve technology solution definitely has the ‘disruptive potential’ of replacing the inflexible mechanical components used so far, while also providing the potential for further and more extensive applications. At every stage of the design process, complying with the specification was our top priority, enabling us to create an optimum solution for the customer’s system.
Our relentless pursuit of excellence sits at the heart of our ability to provide customers across industries with leading-edge engineering solutions.
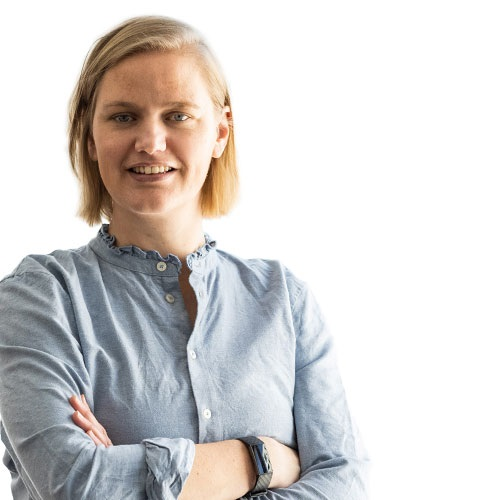