semicon circularity
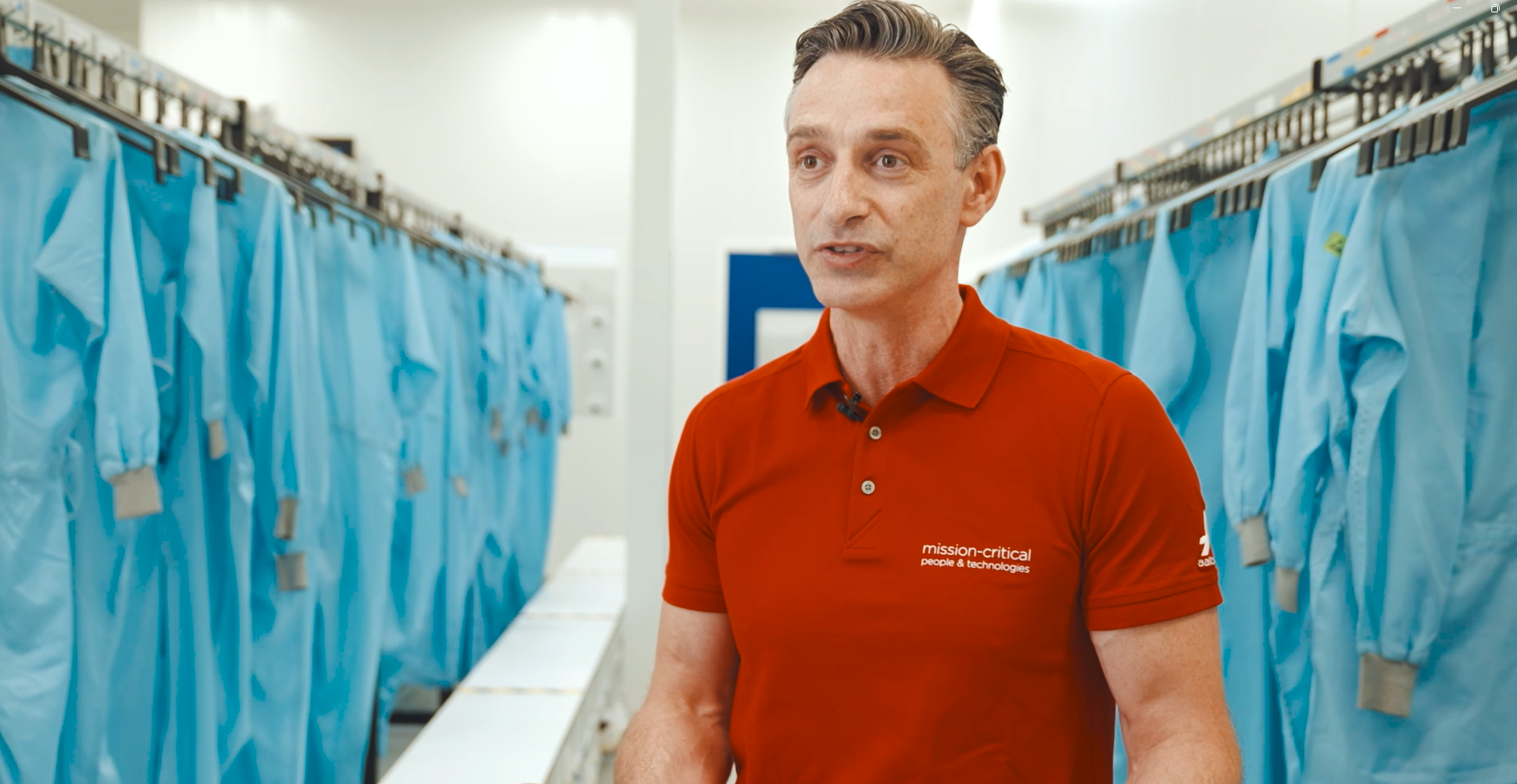
We have a new project which is running with a customer of ours, an SPE producer for OEM equipment and we delivered them a module or a system which is used in their end product. And this big module is coming back to us and we completely take it apart, refurbish, upgrade, repair where necessary and then deliver it back to them so it can be reused into their end system.
The effect of this particular reuse project, circular economy project is that the materials which are being delivered reduce a large volume of waste.
Waste in the material itself, which is being used and reused, but also in the lifetime of a complete product. Because we refurbish and upgrade materials which then have a completely new lifetime again.
There is no difference between a new product and a refurbished product, as we work closely together with our customer in order to determine which specs are very important and need to be met. Actually we do a better job than that. Because often we also upgrade a sub module to the latest level, the latest standard with different components, which leads to an even a better sub-module, than what was delivered in the first place.
We differentiate ourselves on the market because of our long-lasting experience. Not only in manufacturing products, but also our close working relationship with our customers. Going from design to manufacturing to qualification to repair and now actually also doing the reuse is a logical step in the partnership we have with our customers, making the market more circular than before.
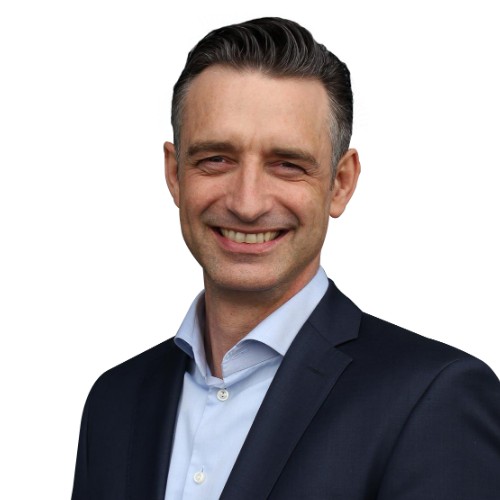