satisfying the demand for HIP solutions
highlights
- Aalberts surface technologies’ recent introduction of a second hot isostatic pressing (HIP) unit at their state-of-the art facility in South Carolina, USA, enables to further expand their service offering and seize new market opportunities
- the addition will help the company meet the needs of industries that demand high quality and quick turns with unrivalled accuracy
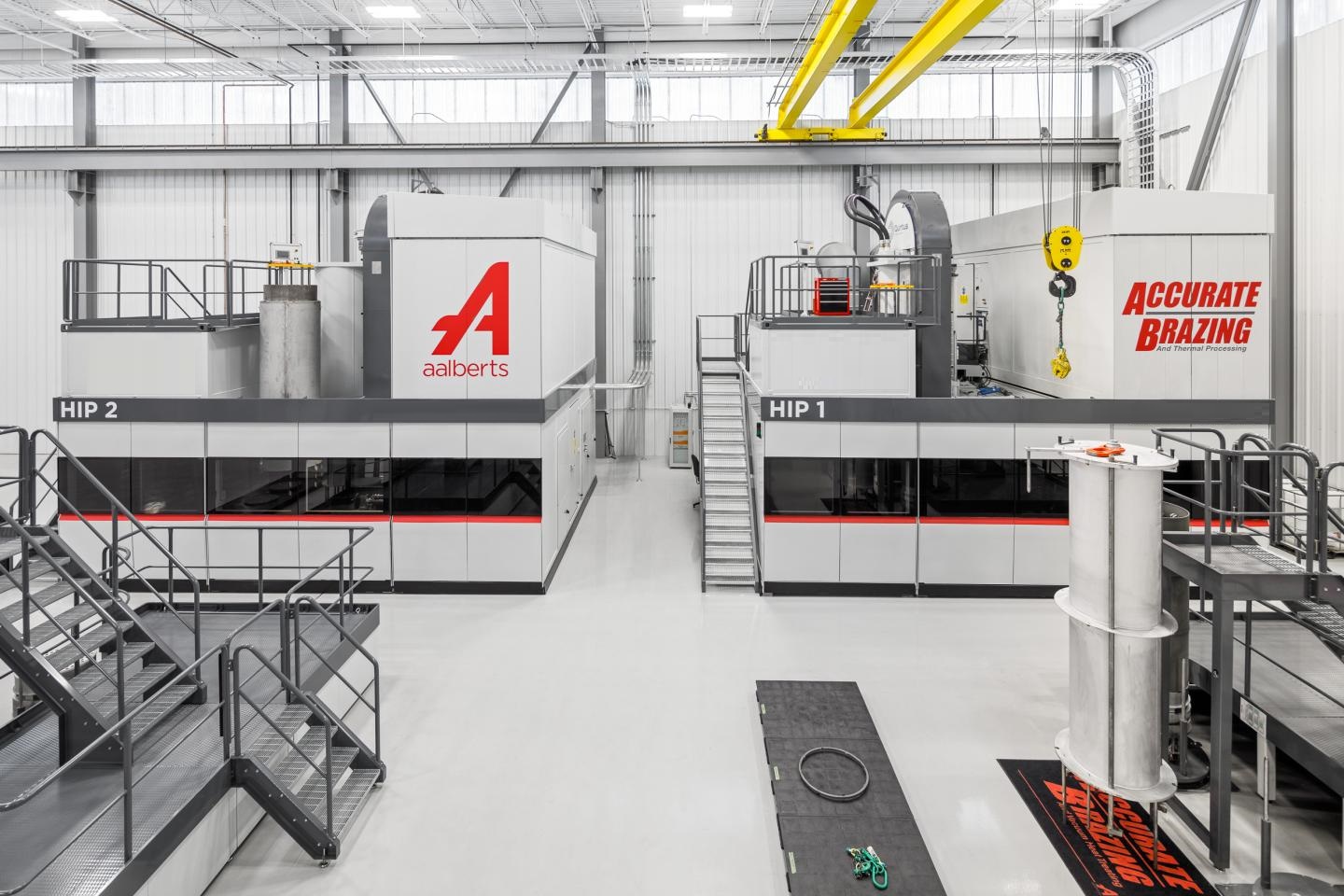
Aalberts surface technologies' recent introduction of a second hot isostatic pressing (HIP) unit at their state-of-the art facility in South Carolina, USA, will enable them to further expand their service offering and seize new market opportunities, as the demand for HIP solutions from customers across a range of industries continues to grow.
latest developments
“We are leading the charge in the supply chain to support additive manufacturing, and investing in a second HIP unit shows our commitment to stay at the forefront to meet the needs of industries that demand high quality and quick turns with unrivalled accuracy,” explains Brent Davis, President, Aalberts surface technologies location Greenville. “Our services are critical for the post-processing of additive manufacturing, and being able to keep these processes under one roof is an important point of difference. This minimises handling of the part and reduces over-all lead time, reducing the number of process steps. Service businesses like ours need to constantly improve their capabilities, especially when it comes to meeting the tight timelines of the aircraft and ground turbine industries. A key aspect of this is industry accreditations, and all of our facilities are Nadcap accredited and ITAR registered. This is critical to serve our aerospace and defence customers.”
customer connection
Connecting with customers remains a vital part of the business, and Aalberts surface technologies was delighted to be able to exhibit at North America’s largest additive manufacturing event in Chicago earlier this month. "This is one of the first shows we have been able to both attend and exhibit at since the pandemic began," Brent says. "We reconnected and made new connections with many industry leaders and we were able to showcase our HIP capabilities, which is a proven technology for heat treatment, consolidation of powder, and removal of porosity from castings."
“This latest HIP unit increases our capacity to meet customer demand for perfect parts”
latest developments
“We are leading the charge in the supply chain to support additive manufacturing, and investing in a second HIP unit shows our commitment to stay at the forefront to meet the needs of industries that demand high quality and quick turns with unrivalled accuracy,” explains Brent Davis, President, Aalberts surface technologies location Greenville. “Our services are critical for the post-processing of additive manufacturing, and being able to keep these processes under one roof is an important point of difference. This minimises handling of the part and reduces over-all lead time, reducing the number of process steps. Service businesses like ours need to constantly improve their capabilities, especially when it comes to meeting the tight timelines of the aircraft and ground turbine industries. A key aspect of this is industry accreditations, and all of our facilities are Nadcap accredited and ITAR registered. This is critical to serve our aerospace and defence customers.”
customer connection
Connecting with customers remains a vital part of the business, and Aalberts surface technologies was delighted to be able to exhibit at North America’s largest additive manufacturing event in Chicago earlier this month. "This is one of the first shows we have been able to both attend and exhibit at since the pandemic began," Brent says. "We reconnected and made new connections with many industry leaders and we were able to showcase our HIP capabilities, which is a proven technology for heat treatment, consolidation of powder, and removal of porosity from castings."
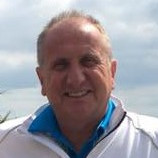
any questions?
Brent Davis
president
at Accurate Brazing
Accurate Brazing